Obra GPNK: Soluciones para cada decisión estratégica
Sobre el final de la obra del Gasoducto Presidente Néstor Kirchner diseñamos una novedosa solución para realizar el secado de la tubería desde varios frentes a la vez: compresores eléctricos montados en distintos semirremolques capaces de operar en forma conjunta. Sumado a esto, los equipos hicieron funcionar las plantas doble junta y los robots automáticos de soldadura, dos instalaciones que resultaron clave para acortar los plazos de construcción y lograr llevar adelante este proyecto en tiempo récord.
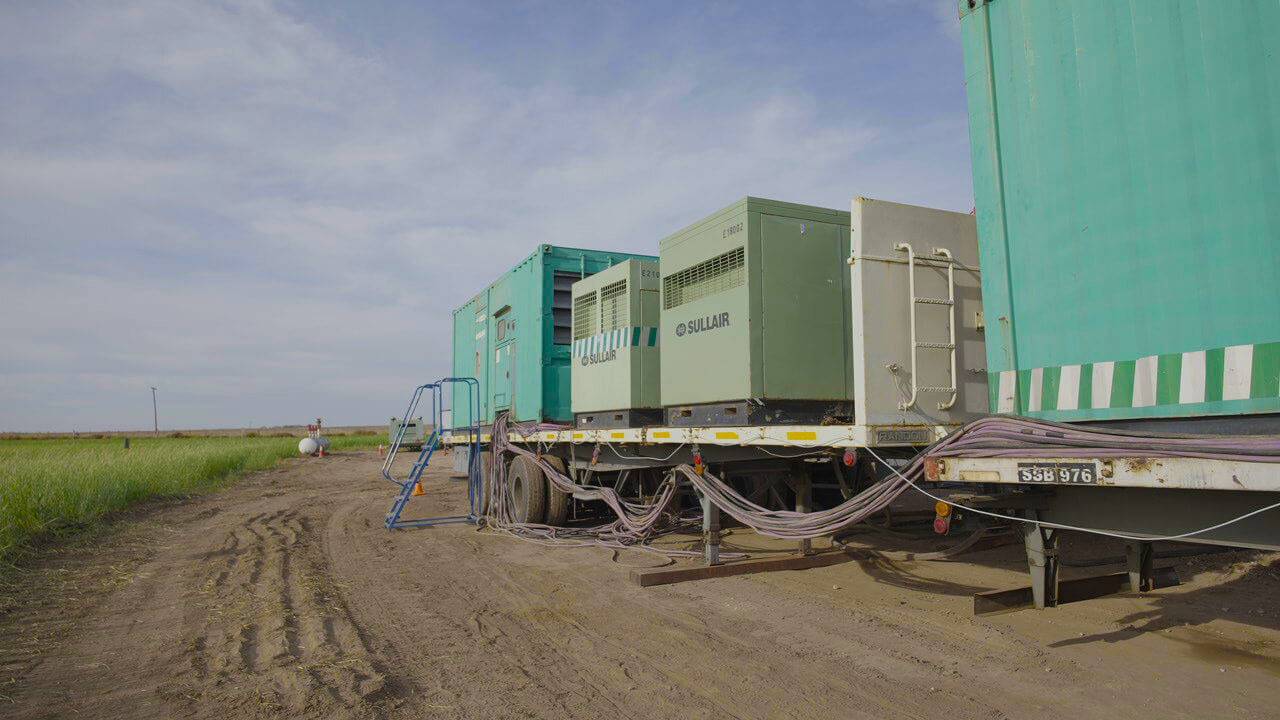
En la recta final de la obra GPNK hubo una decisión estratégica sobre cómo realizar el secado de la tubería: sumar varios frentes de secado de manera tal de poder imprimirle mayor velocidad a la tarea. Esto motivó a Sullair Argentina a idear rápidamente una solución a medida que pudiera dar respuesta a esa necesidad. Y la novedosa propuesta resultó sumamente eficaz: compresores eléctricos organizados en semirremolques con grupos electrógenos.
“Hicimos una propuesta novedosa desde la técnica. Frente a la cantidad de equipos que se necesitaban para una tarea semejante, propusimos un sistema de secado diseñado con compresores eléctricos y con grupos electrógenos, todo esto montado sobre distintos acoplados”, explica Gustavo De Girolamo, Gerente de Servicios. Estar presentes en el lugar fue fundamental para dimensionar el desafío y diseñar, entre el área de logística y la de servicio técnico, la mejor solución para ese reto.
Se armaron distintas baterías de compresores eléctricos montados sobre semirremolques de 12 metros cada uno. Fueron tres los semirremolques armados. Cada uno de ellos con un grupo electrógeno y con dos -o tres- compresores de aire. El diseño de este sistema de secado permitió el trabajo de forma individual y también conjunta.
Acompañamos estratégicamente durante todo la construcción
Durante todo el período de la construcción del gasoducto acompañamos cada una de las decisiones estratégicas pensadas para acelerar los tiempos de producción, buscando siempre que el cliente pudiera lograr su objetivo: culminar la obra en tiempo récord.
Aportamos la energía que le dio vida a las plantas doble junta, que fueron cambiando de ubicación a medida que avanzaba la obra. Y fuimos también los responsables de la energía que movió todo un proceso de soldadura robótica única en el país: tres robots en la línea trabajando en forma alternada soldando por dentro y por fuera.
Las plantas doble junta y estos robots de soldadura fueron esenciales para los tiempos del proyecto; con ellos se logró alcanzar una productividad diaria de entre 4.5 y 5 kilómetros.
Que los equipos, las soluciones a medida y la presencia permanente en obra de los especialistas técnicos hayan asegurado esa productividad récord refleja nuestra misión primera: poder transformar aquello que era un objetivo en una realidad.
COMENTARIOS
Respuesta para Juan