Inédito caudal de aire comprimido entregado al mismo tiempo
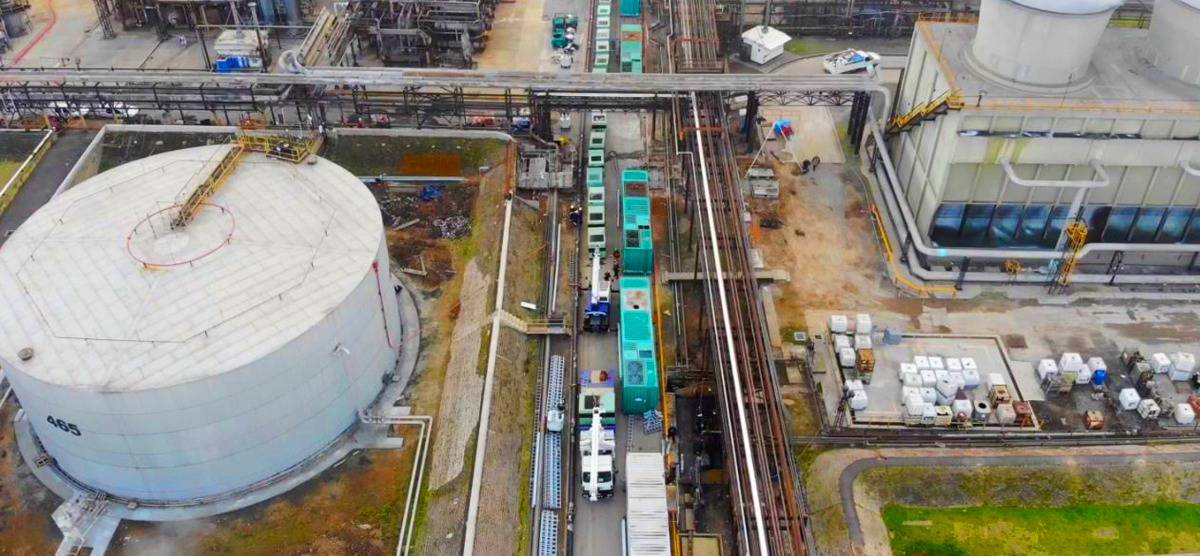
En un hecho sin precedentes en América Latina, la planta de refinería de petróleo PanAmerican Energy continuó funcionando sin su soplador principal gracias al servicio de Sullair Argentina quien entregó, ininterrumpidamente y durante un mes, 1000 m³/min de aire comprimido a una presión constante de entre 5 y 6 bar.
En plena pandemia de COVID-19, nuestro equipo de alquileres recibió un requerimiento inédito: proveer durante un mes 1000 metros cúbicos de aire comprimido por minuto, con una presión constante de entre 5 y 6 bar. Semejante solicitud no tenía antecedentes en América Latina: jamás se había entregado antes, en un mismo punto de generación, en el mismo lugar y al mismo tiempo tanto caudal de aire comprimido.
El pedido llegó de la mano de PanAmerican Energy para su planta de refinería de petróleo ubicada en Campana, provincia de Buenos Aires. ¿Qué había sucedido? El soplador principal de su unidad de craqueo catalítico - que es justo donde se producen las naftas y gasoil - necesitaba ser reparado. Tenían dos alternativas. Una, la tradicional: parar la planta completamente y reparar el soplador. La otra, inédita y sumamente ambiciosa: conseguir quien fuera capaz de reemplazar el aire provisto por el soplador y proveer semejante suministro de aire sin detener, ni siquiera por un segundo, el funcionamiento de la planta. Sullair Argentina era la única compañía capaz de asumir este desafío y brindar la solución. Y así lo hicimos.
De un desafío único a un servicio extraordinario
Para lograr el objetivo se necesitaron varios compresores de aire en línea trabajando en forma ininterrumpida, por lo que prácticamente todos los equipos disponibles de la flota, más de 60 entre eléctricos y diésel, fueron adjudicados a este trabajo. Desde luego, la refinería no tenía previsto dar energía a más de medio centenar de compresores funcionando al mismo tiempo, de manera tal que también fue necesario instalar grupos electrógenos y tanques de combustible.
El despliegue incluyó la colocación de tableros de distribución específicos en las terminales y torres de iluminación para operar durante los horarios nocturnos. El sitio en sí mismo y la pandemia fueron otro desafío. Por la falta de espacio y el acceso limitado iba a ser imposible cambiar un equipo en caso de alguna falla. Así las cosas, cada compresor tendría su backup. Todos los equipos trabajarían al 50% y subirían su capacidad al 100% al momento de sacar a su par de servicio por mantenimiento o cambio de aceite y filtros.
La logística implicó el despliegue de 20 camiones para el traslado de maquinaria y la instalación entera llevó un mes. Todo el personal involucrado, además, debió seguir estrictos protocolos sanitarios debido a la pandemia.
El simulador, un as bajo la manga
Poner en marcha un sistema tan complejo y delicado requería el manejo de muchas variables simultáneas, así que cada posible contingencia fue prevista de antemano con una herramienta clave: un simulador que proyectó todos los escenarios posibles: Fallas en los compresores, paradas para mantenimiento, fallas de ambos grupos electrógenos con la consecuente parada repentina de 12 compresores a la vez o el impacto que podrían tener en el equipo ciertas fluctuaciones de la temperatura. Todo, absolutamente todo, estaba previsto de antemano gracias al simulador.
El pase: respaldo, precisión y estabilidad
La entrada de todo el sistema a la torre de craqueo debía hacerse en forma simultánea y coordinada con la retirada del soplador para que el volumen de aire no sufriera alteraciones. A medida que el soplador se fue apagando, se fue abriendo la válvula para que el aire de los equipos fuera reemplazando paulatinamente al aire del soplador. La precisión del proceso implicó calibrar y regular las máquinas y válvulas de la línea para entregar el aire en el punto de consumo a una presión, 2 kg por cm², algo muy inferior a lo habitual.
Reparado el soplador de la refinería, se realizó la secuencia inversa. Se reconectó el equipo, se lo encendió y se fueron apagando los compresores de aire según era necesario para que la provisión de aire fuera uniforme y continua.
Fueron 25 días de servicio de provisión de aire de manera interrumpida. Y fue un éxito rotundo en todo sentido. El trabajo involucró prácticamente todas las áreas de la compañía. Trabajar en conjunto con un objetivo común es algo ya característico de Sullair Argentina. Y es eso lo que garantiza el éxito de los proyectos.
Los números detrás del éxito
- 30 días de instalación
- 43 compresores eléctricos entre 470 y 1120 CFM
- 20 compresores diésel de entre 750 y 1300 CFM
- 8 grupos electrógenos entre 2000 y 2500 kva
- +500 toneladas de equipos
- 2 tanques con 50.000 litros de gasoil
- +6 kilómetros de cables tendidos
- 300 metros en línea de equipos
COMENTARIOS
Respuesta para Juan